Our Mission
Introducing the Smart Knob for Autonomous Burner Supervision
The Aspire system requires minimal user management and introduces the Smart Knob to collaborate with kitchen appliances lacking built-in connectivity features. The autonomous solution supervises burners, significantly improving safety. Our team developed the product internally.
01. Project Planning
Starting the Design
In the Aspire system, the Smart Hood and the Smart Knob are two main products. I led the design of the Smart Knob, a crucial component of our project. Our primary objective was to design a Smart Knob that would embody our vision for the future. Collaborating with a mechanical engineer who developed the internal knob mechanism, I was responsible for designing the knob housing and integrating the LED lights.

FF1: Smart Hood
Contextually aware system
with targeting ventilation

FF2: Smart Knob
Mechanical automation and safety
02. Competitor Research
Finding New Design Opportunities
Conducting usability research, I tested various smart knobs in the market to identify what could make Aspire unique and better. The key design takeaway was that Aspire should seamlessly blend into everyday kitchens with a premium look and compact dimensions.

Design Challenge
Designing the Smart Knob Housing for Optimal Human Interaction
Designing the housing for the Smart Knob presented a challenge: merging a futuristic aesthetic with optimal human interaction. Our goal was to make the Smart Knob visually distinct as an autonomous device while ensuring minimal user engagement. The solution needed to facilitate easy and secure turning on and manual control through efficient grip, rotation, and push interactions.
03. Design Development
Deciding Design Theme Direction
Form Development
Initially, we aimed to create a design that reflects boldness, intuitiveness, and a premium feel. Together with ME, we determined the dimensions of the design.
Then, we explored two design options, one with a nose and one without. We carefully evaluated the pros and cons of each option and ultimately decided to proceed without the nose.
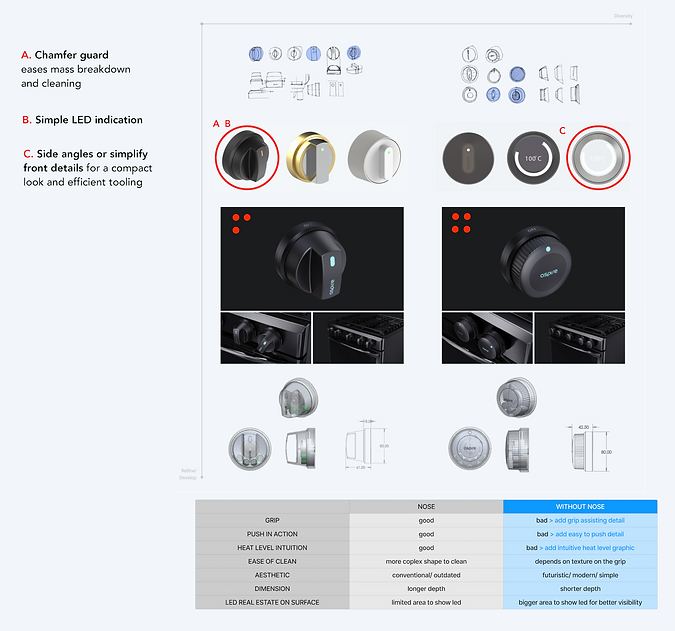
Design Iterations
I revised several versions of the no-nose form factor by integrating futuristic and discreet LED lights and testing the grip with 3D-printed prototypes. The team reviewed the designs based on specific criteria and selected the final design. However, the surface of the final design needed improvement to provide a better grip and enable rotation for the users.

1. Futuristic Form Factor:
👍 ✓✓✓✓
✓✓✓
✓✓
✓
2. Discreet LED:
3. Harmonious:
4. Grip & Rotate:
👍 ✓✓✓✓
👍 ✓✓✓✓
✓✓✓✓
✓✓✓
✓✓✓
👎 ✓✓✓
✓✓
✓✓
✓✓
✓
✓
✓

04. Testing and Refining
Updating Design Details
We updated surface details to improve grip and tested LED diffusion methods that could maintain discreetness through back-and-forth communication with internal ME and overseas vendors.



01. Surface update
Updated surface to better grip and simplified the design pattern, extending from the form's edge to the middle of the side body to align with horizontal heat-level graphics.
02. LED diffusion brainstorming
Explored using a shallow-walled internal surface with a LED lighting diffusion, eliminating the need for a parting line.
03. Inquiry to vendors
Inquired with vendors, shared housing drawings. They can CNC both ABS and Aluminum for cosmetic purposes but need a separate lighting pipe for Aluminum.
After revising the design, I ordered the initial cosmetic housing in both aluminum and ABS and then tested the LED diffusion results.
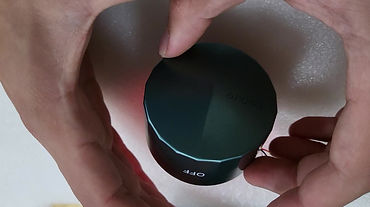


01. Testing LED with ABS
Appeared seamless, but dark color options exhibited paint speckles when the LED is on.
02. Testing LED with Aluminum + Light pipe
Tried painting the outer light pipe to match the housing, but it had paint speckles when the LED was on. The thin light pipe also had rotational stability issues
03. Light Pipe Redesign
Expanded the light pipe's dimensions for security and maintained the raw diffuser material to ensure consistent lighting.
05. CMF Design
Match with Brand Language

Objective
Our goal was to achieve a fingerprint-resistant, secure-grip finish, select colors that complement universal CMF (metal, monochrome, etc.), provide clear and intuitive heat indication, and incorporate a subtle logo design.
Considering the knob's potential inclusion in the Bespoke brand line, we aimed to offer customization through material options and various color choices. We ordered product variations for the initial review phase.

CMF Evaluation
After receiving prototypes, we conducted CMF review, and finalized CMF options: black, red, green, beige colors, and AL and ABS materials. Proposed these in the project proposal to HQ and during the demo.

✓
✓
✓
✓

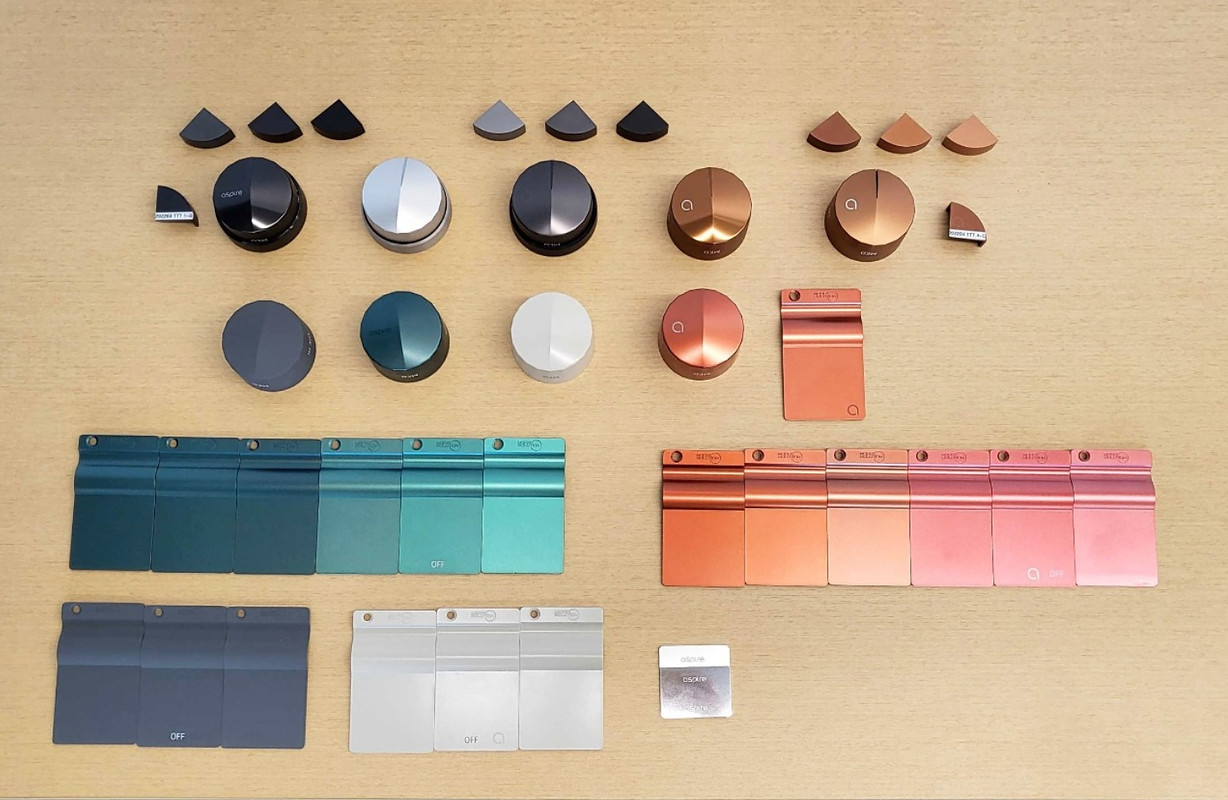
06. Integrating Prototypes
Making it Work
I helped build the Aspire kitchen setup to test its automation. We integrated UI screens with devices to test the auto-shutoff feature triggered by hood over-boiling detection. The system review was comprehensive and allowed for a user-centric perspective. This led to feedback updates such as LED blink patterns and audio cues preceding the auto shut-off from the knob.
